Risikobeurteilung - Identifizieren von Gefährdungen
Einleitung
Die Risikobeurteilung ist ein Kernpunkt der Maschinenrichtlinie und bei Herstellern das wahrscheinlich leidigste Thema. Doch warum ist das so? Auf der einen Seite ist es natürlich selbstverständlich, dass ein Hersteller ein sicheres Produkt auf den Markt bringen möchte. Auf der anderen Seite steht dem Sicherheitsgedanken der scheinbar große Aufwand der Risikobeurteilung entgegen, der gefühlt keinen weiteren Beitrag zur Produktentwicklung liefert. Da wir uns in diesem Artikel überwiegend auf die Maschinenrichtlinie beziehen, und diese von Maschinen und nicht von Produkten spricht, möchten wir im folgenden auch diesen Begriff verwenden.
In vielen Unternehmen ist dies tatsächlich gefühlt auch der Fall, denn wenn eine Maschine entwickelt wird und eine Risikobeurteilung erst im Anschluss durchgeführt wird, muss diese unweigerlich eine Nachdokumentation der Maschine sein. Und eine Nachdokumentation fühlt sich wahrlich nicht effektiv und produktiv an. Viel schlimmer wird es, wenn die Maschine dann tatsächlich auch noch umgebaut werden muss. Es liegt bekanntlich in der menschlichen Natur, dass dieser zusätzliche Aufwände scheut und versucht den kürzesten Weg zu gehen, auch wenn dieser in eine Sackgasse führt. Zu dem ganzen Dilemma kommt auch noch hinzu, dass die Anwendung von Normen und Richtlinien an den Universitäten und Hochschulen wenig bis gar nicht unterrichtet werden. Die Realität ist hier leider, dass die Unternehmen auf sich allein gestellt sind.
Gesetz ist jedoch Gesetz, da kommen wir nun mal nicht drum herum, also müssen wir diese Risikobeurteilung machen. Die Frage die sich jedoch stellt ist, wie lösen wir das oben beschriebene Problem auf? Eine Antwort kann sein, dass wir uns eine Methode zurecht legen, welche die Risikobeurteilung in den Entwicklungsprozess integriert. Die Integration muss so erfolgen, dass die Risikobeurteilung über den Prozess verschwimmt und nicht heraus lösbar ist. Zusätzlich soll das Ergebnis der Risikobeurteilung einen erheblichen Anteil zur Lösung beitragen.
Ansonsten gilt trotzdem, ohne Fleiß kein Preis. Die erforderlichen Normen müssen gelesen und verstanden werden. Unter der Maschinenrichtlinie ist die Norm EN 12100 als Leitfaden für die Durchführung einer Risikobeurteilung harmonisiert. Wir können Ihnen hier wirklich nur ans Herz legen, sich mit dieser Norm zu beschäftigen und die für Sie relevanten Methoden von dort abzuleiten. Dies gilt selbstverständlich auch für die Richtlinien, die auf die Maschine Anwendung finden können, denn es gibt neben der Maschinenrichtlinie auch andere.
Begriffe
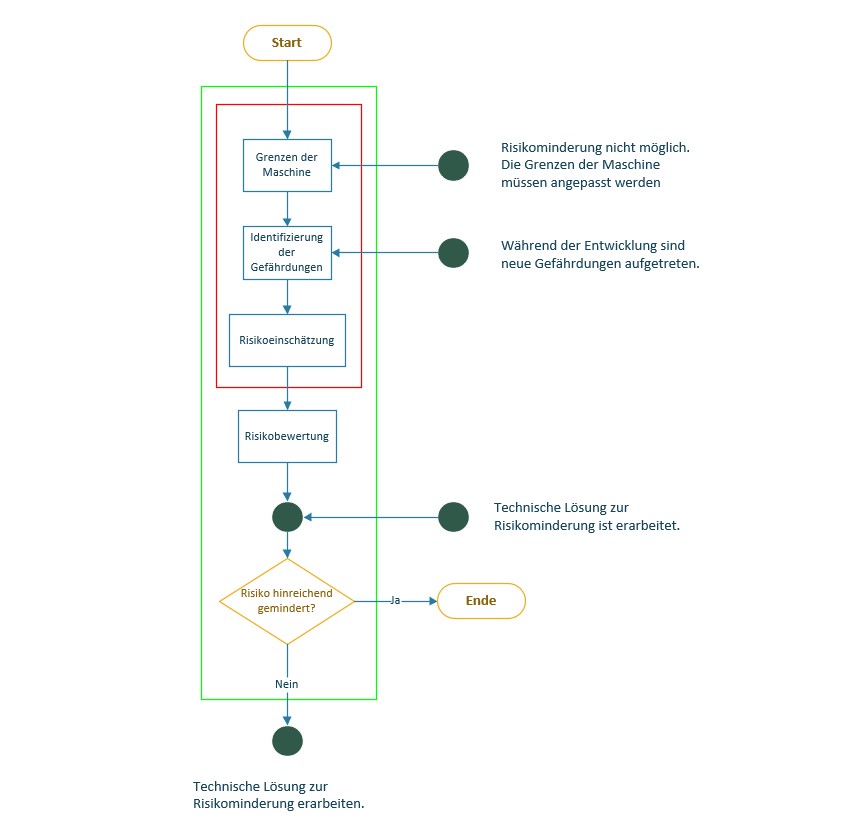
Bevor wir in den folgenden Kapiteln ins Detail gehen, möchten wir kurz einige Begriffe auffangen, die in der Praxis doch häufig zur Verwirrung führen.
Risikoanalyse:
Die EN 12100 sieht vor die Risikobeurteilung mit den Grenzen der Maschine zu beginnen und im Anschluss die Gefährdungen, Gefährdungsereignisse und Gefährdungssituationen zu identifizieren.
Die identifizierten Gefährdungssituationen müssen dann auf ihr Risiko bzgl. Schadensausmaß und Eintrittswahrscheinlichkeit eingeschätzt werden.
Diese drei Prozess-Schritte werden als Risikoanalyse bezeichnet. In der Abbildung oben ist die Risikoanalyse mit einem roten Rahmen gekennzeichnet.
Risikobewertung:
Die Risikobewertung hat die Aufgabe auf der Grundlage der Risikoanalyse zu entscheiden ob eine identifizierte Gefährdung relevant oder signifikant ist.
Bei einer signifikanten Gefährdung muss die Entwicklung entsprechende Maßnahmen definieren und umsetzen, die zu einer Risikominderung führen.
Risikobeurteilung:
Die Risikobeurteilung enthält die Risikoanalyse und Risikobewertung ergänzt um die Beurteilung, ob eine geplante Maßnahme zur Risikominderung korrekt umgesetzt wird.
Damit ist die Risikobeurteilung ein stark iterativer Prozess, der seine Ergebnisse in die Entwicklung gibt und über eine entsprechende Rückmeldung die entsprechende Kontrolle durchführt.
Die Risikobeurteilung ist in der Abbildung oben mit einem grünen Rahmen gekennzeichnet.
Gefährdungsbeurteilung:
Die Gefährdungsbeurteilung ist für den Hersteller bzgl. der Inverkehrbringung einer Maschine nur insofern von Bedeutung, dass er die Restrisiken der Maschine angeben muss.
Die Gefährdungsbeurteilung selbst ist durch den Betreiber der Maschine durchzuführen.
Die dazu erforderlichen Informationen holt er sich jedoch aus der Betriebsanleitung des Herstellers, der gemäß Maschinenrichtlinie 2006/42/EG die Restrisiken dort angibt.
Restrisiken sind Risiken der Maschine, die trotz der ergriffenen Maßnahmen nicht vollständig minimiert werden konnten.
Hier kann jedoch der Betreiber z.B. durch weitere Schutzmaßnahmen oder auch organisatorischen Maßnahmen weiter Abhilfe schaffen.
Wo fangen wir an?
Der Anfang ist bekanntlich am schwersten. Die Maschinenrichtlinie fordert ja, dass die Risikobeurteilung mit der Planung beginnt und die Maschine nach den Ergebnissen der Risikobeurteilung zu fertigen ist. Halten wir uns also noch mal vor Augen, was das Ziel der Risikobeurteilung ist. Ein sicheres Produkt bzw. eine sichere Maschine. Wann ist eine Maschine sicher? Wenn es mit der Maschine zu keiner Gefährdungssituation kommen kann! Das Wort "keiner" ist hier mit etwas Vorsicht zu genießen, denn auch die Maschinenrichtlinie lässt ein gewisses Restrisiko zu. Darauf kommen wir jedoch später noch zu sprechen.
Gefährdungssituation
Wir wollen also Gefährdungssituationen vermeiden. Um Sie vermeiden zu können, müssen wir sie natürlich vorher identifizieren. Nur um sichere zu gehen, dass ein gemeinsames Verständnis für den Begriff Gefährdungssituation herrscht, möchten wir eine Definition formulieren.
Definition:
Eine Gefährdungssituation, ist eine Situation, in der sich eine Person befindet, wenn sie einer oder mehrerer Gefährdungen ausgesetzt ist, die bei einem oder mehreren bestimmten Ereignissen eintreten können.
Um eine Gefährdungssituation also identifizieren zu können, ist die Kenntnis über die möglichen Gefährdungen als auch den möglichen Ereignissen die an dem Produkt auftreten können erforderlich. Jetzt stellt sich noch die Frage, warum ist denn die Person überhaupt an dem Ort an dem eine Gefährdung herrscht? Ganz einfach. Sie geht einer bestimmten Tätigkeit nach, damit z.B. die Maschine seine Aufgabe erfüllen kann. Wenn sich die Person nicht gerade verlaufen hat, dann ist dies eines der Hauptgründe, warum sich Personen an bestimmten Positionen aufhalten.
Fassen wir nochmal zusammen. Die Gefährdungssituation ist eine Kombination aus:
- Tätigkeit an einem bestimmten Ort (z.B. Einführen eines Werkstückes in eine dafür vorgesehen Öffnung)
- Gefährdung (z.B. elektrischer Schlag)
- Gefährdungsereignis (z.B. indirektes Berühren)
In diesem allgemeinen Beispiel würde die Person ein Werkstück in eine der dafür vorgesehen Öffnung einführen wollen. Aufgrund eines Fehlers in der Elektrik, steht das Gehäuse jedoch unter Spannung. Beim Einführen berührt die Person zufällig das Gehäuse und ein elektrischer Schlag ist die Folge.
Doch kommen wir nochmal zurück zu unserer ursprünglichen Frage. Wo fangen wir an?
Der Anfang
Bei der Aufgabe selbstverständlich!
Denn sie ist für die Maschine der Sinn des Lebens und der eigentliche Grund warum der Kunde sie erwerben möchte.
Damit ist die Aufgabe, welche die Maschine erfüllen soll, der Ursprung und Startpunkt der Risikobeurteilung.
Die Aufgabe des Produktes
Wie wie oben erkannt haben, leitet sich für die Risikobeurteilung viel von der Aufgabe der Maschine ab. Jedoch nicht nur für die Risikobeurteilung. Wir wagen es, uns zu sagen, dass dies für die Produktentwicklung selbst unerlässlich ist. Ganz davon zu schweigen wenn es am Ende um eine Abnahme der Maschine geht.
Die Anzahl der Aufgaben die eine Maschine zu erfüllen hat,ist meist überschaubar. Wir reden hier in den meisten Fällen von 1 - 3 Aufgaben, die sich evtl. nochmal in Teilaufgaben untergliedern lassen. Wichtig ist jedoch, dass Sie sich der Aufgaben bewusst sind und sie exakt definieren. Die Art der Definition verhält sich ähnlich wie die der Zieldefinition.
- Spezifische Beschreibung
- Messbarkeit
Spezifische Beschreibung
Wir beschreiben jede Aufgabe, welche die Maschine erfüllen soll. Bitte jedoch nicht wie die Aufgabe zu erfüllen ist: Denn das wie gehört üblicherweise bei der Produktentwicklung an eine andere Stelle, dazu später mehr. Mit spezifisch ist gemeint, dass wir die Formulierung so ausführen, dass kein Spielraum mehr für Interpretationen besteht. Wenn wir dann aus dem Schreiben nicht mehr herauskommen, ist das meist ein Anzeichen dafür, die Aufgabe in weitere Teilaufgaben zu untergliedern. Als Ergebnis erhalten wir zum Schluss eine Aufgabenstruktur in einer Art Organigramm.
Messbarkeit
Nachdem wir beschrieben haben was die Maschine im Detail machen soll, wollen wir auch definieren, woran wir erkennen, dass die Aufgaben auch richtig durchgeführt werden. Glücklicherweise müssen auch die Aufgaben einer Maschine den physikalischen Gesetzen folgen, womit sich dann auch die physikalischen Größen als Indikator anbieten. Bei solchen Angaben sind natürlich auch die Messunsicherheiten anzugeben.
Kurzes Fazit
Wir haben also erkannt, dass sich bei der Produktentwicklung vieles von der Aufgabendefinition der Maschine abhängt und sich ableiten lässt. Damit haben wir hier den ersten Synergie-Effekt gefunden, bei dem sich herausstellt, dass eine Verschmelzung zwischen Risikobeurteilung und der eigentlichen Entwicklung möglich ist. Doch wie geht es nun weiter? Was machen wir jetzt mit diesen Informationen? Wir überlegen uns, wie die Maschine die Aufgabe umsetzen soll. An dieser Stelle kommen nun die Funktionen der Maschine ins Spiel.
Die Funktionen der Maschine
Die Ausarbeitung der Funktionen ist ein Kernthema der Produktentwicklung für die es mehrere auch in der Literatur beschriebene Ansätze gibt. Sie ist jedoch auch ein maßgeblicher Teil der Risikobeurteilung, denn nur wer weiß, wie seine Maschine funktioniert, kann diese auch wirklich bewerten.
Was ist eine Funktion?
Vorab. Der Sinn der Funktion besteht rein darin, die Maschine dazu zu befähigen, ihre Aufgabe richtig zu erfüllen. Damit besteht immer ein direkter Zusammenhang zwischen Funktion und Aufgabe der Maschine. Doch was ist nun eine Funktion?
Definition:
Wir erinnern uns an den Mathematikunterricht als wir das erste mal die Formel y=f(x) gesehen haben.
Eine Funktion hat eine Eingangsgröße x bearbeitet diese und gibt die Ausgangsgröße y wieder aus.
Im Anlagenbau und damit für Maschinen typisch können diese Größen von folgendem Typ sein:
- Energie
- Stoff
- Signal
Funktionsstruktur
Die Funktionsstruktur bildet alle Funktionen in ihren Abhängigkeiten ab. Um also eine Aufgabe zu erfüllen, werden meistens mehrere Funktionen miteinander verkettet. Verkettet soll bedeutet, dass eine Funktion eine Eingangsgröße x erhält sie in die Ausgangsgröße y wandelt und mindestens einer Funktion wieder als Eingangsgröße übergibt. Damit ist die Verkettung immer entlang des Energie-, Stoff- oder Signalflusses vorhanden.
Das ist Perfekt, sowohl für die Risikobeurteilung als auch für die Produktentwicklung. Mit einer solchen Struktur können wir in drei Ebenen abtauchen:
Abstrakt:
Die abstrakte Darstellung einer Funktionsstruktur besteht im Grunde aus Kreisen und Vierecken.
Die Vierecke beinhalten die Funktion selbst, die in ihrer Benennung aus einem Nomen und einem Verb besteht.
Die Kreise sind die Eingangs- und Ausgangsgrößen.
Der Vorteil der abstrakten Darstellung ist im Grunde die einfache Darstellung und die Möglichkeit, sich von einer bestimmten technischen Lösung zu trennen.
Zusätzlich ist die Funktionsstruktur wie eine Landkarte und gibt einen doch recht guten Überblick über das Gesamtsystem.
Mit ihrer Eigenschaft das System entlang des Energie-, Stoff- oder Signalflusses zu beschreiben, ist sie ein idealer Leitfaden für die Risikobeurteilung.
Physikalisches Prinzip:
Jeder Funktion kann mindestens ein physikalischer Prinzip zugewiesen werden.
Auch dieses Prinzip gibt noch keine genauen Einblick auf die technische Lösung, wir wissen jedoch schon mal mit welchen physikalischen Größen wir es zu tun haben.
Der Produktentwicklung hilft die Art der Beschreibung mehrere Lösungen vor zu entwickeln um dann mittels einer Bewertung die optimale Lösung zu bestimmen.
Für die Risikobeurteilung bedeutet dies, dass wir bis zu einem bestimmten Punkt bereits Kenntnis von den möglichen Gefährdungen haben.
Diese möglichen Gefährdungen sollten in der Produktentwicklung als Bewertung für die Lösungsfindung einfließen.
Damit werden wir der Forderung der Maschinenrichtlinie mehr als gerecht, da die ersten Ergebnisse bereits einfließen, bevor die technische Lösung entstanden ist.
Technische Lösung:
Jedem physikalischen Prinzip kann mindestens eine technische Lösung zugewiesen werden. Hier entstehen dann bereits die ersten schematischen Zeichnungen, sowie die Auswahl der Komponenten, inkl. der Dimensionierung.
Spätestens ab hier kann aus Sicht der Risikobeurteilung bereits mit einer FMEA (Fehlermöglichkeits- und -einflussanalye) begonnen werden.
Auf Basis der Bauteile können Fehlermöglichkeiten identifiziert und beschrieben werden.
Auch hier sind die Ergebnisse der Risikobeurteilung eine gute Grundlage für die Produktentwicklung.
Besonders freuen wird sich auch der Service, wenn eine gute Beschreibung der Fehlerfälle vorliegt und die Maßnahmen ebenso durchdacht sind.
Diese drei Ebenen lassen uns in der Risikobeurteilung leicht zwischen dem großen Überblick und dem Detail in einer Funktion hin und her springen. Damit ist uns ein roter Leitfaden gegeben, bei dem wir selbst bei größeren Änderungen an der Anlage den Überblick behalten.
Nun sind die Funktionen einer Maschine jedoch nur die halbe Miete. Denn die Funktionen alleine befähigen die Maschine nur, die entsprechende Aufgabe zu erfüllen. Sie benötigen einen Anstoß von außen, die den Funktionen mitteilt wann, wie lang und in welcher Reihenfolge sie aktiv werden sollen. Wir wollen dafür den Begriff Tätigkeiten verwenden.
Die Tätigkeiten an einer Maschine
An wahrscheinlich jeder Maschine muss der Bediener und die Maschine selbst mindestens eine Tätigkeit ausführen um die Funktionen der Maschine in Gang zu setzen. Dafür kann es auch erforderlich sein, die Tätigkeiten in einer bestimmten Reihenfolge auszuführen. Wichtig zu verstehen ist, dass eine Tätigkeit nicht nur über eine Person ausgeführt werden kann, sondern auch durch die Maschine selbst. Besonders interessant wird es dann, wenn die Tätigkeiten von Mensch und Maschine interagieren.
Was ist eine Tätigkeit?
Eine Tätigkeit ist im Grunde eine Handlung die dazu führt, dass eine oder mehrere Funktionen ausgeführt werden. Erzeugen diese ein Zwischenergebnis ist eine weitere Tätigkeit erforderlich um die nächsten Funktionen auszuführen.
Wir wollen dies an einem kleinen Beispiel erläutern:
Wir wollen z.B. Kühlwasser durch einen Wärmetauscher fahren.
Dazu haben wir eine Pumpe die das Wasser aus einem Tank bezieht.
Dieser Tank kann wiederum über eine andere Pumpe aus einem großen Vorratsbehälter befüllt werden.
In diesem Beispiel können wir drei Tätigkeiten ausführen:
- Tank befüllen
- Kühlung starten
- Kühlung anhalten
Aus technischer Sicht spielt es zunächst keine Rolle wer diese Tätigkeiten ausführt. Wir nehmen erst mal an, dass der Tank leer ist. Es kann also entweder der Benutzer die Tätigkeit Tank befüllen ausführen oder die Maschine selbst, in dem z.B. der Schwimmer anschlägt. Auch die nächste Tätigkeit, die dazu führt das die Pumpe das Kühlwasser durch den Wärmetauscher wälzt, kann z.B. durch den Bediener erfolgen oder durch die Maschine selbst, in z.B. der Schwimmer anschlägt und die Pumpe startet, da der Tank ja nun voll ist.
Abläufe an einer Maschine
Wenn wir nun alle erforderlichen Tätigkeiten aufschreiben, können wir sie je nach Abhängigkeit in eine bestimmte Reihenfolge setzten. Aus dieser Zusammensetzung entsteht nun ein Ablauf. Dank der Ablaufbeschreibung wissen wir nun, wann sich wer wo aufhält, wenn die Maschine bestimmungsgemäß verwendet wird. Diese Information ist für die Risikobeurteilung Gold wert und dient der Produktentwicklung ebenfalls als Bewertungsgrundlage für die Auswahl der technischen Lösung als auch der Prozessoptimierung des Produktes. Denn wie bekannt Zeit ist Geld.
Die Maschinenrichtlinie fordert jedoch nicht nur die Betrachtung der bestimmungsgemäßen Verwendung, sondern auch die Betrachten der vorhersehbaren Fehlanwendung. Für den Ablauf bedeutet das, dass wir uns tatsächlich noch überlegen müssen, auf was für tolle Ideen der Benutzer der Maschine bei seinen Tätigkeiten noch kommen kann, die wir so nicht vorgesehen haben. Der Grund warum die Maschinenrichtlinie dies fordert, liegt auf der Hand. Es ist rein menschlich, dass der Anwender einer Maschine sein Verhalten so anpasst, dass der Nutzen maximal und der Widerstand minimal ist. Dieses Verhalten kann dann leider von der bestimmungsgemäßen Verwendung, bzw. vom Entwickler vorgesehenem Ablauf abweichen.
Mit dem Fortschritt der Planung kennen wir nun die erforderlichen Funktionen, als auch die Abläufe an der Maschine. Damit kann nun auch die Risikobeurteilung im vollen Umfang aufgesetzt werden. Parallel hierzu beginnt auch die Detail Konstruktion für die Maschine.
Aufsetzen der Liste der identifizierten Gefährdungen
Wir erinnern uns kurz an unser Ziel ein sicheres Produkt auf den Markt zu bringen, in dem wir Gefährdungssituationen vermeiden möchten. Dazu gilt es nun, mittels den Informationen die wir haben, die Gefährdungssituationen zu ermitteln.
Gefährdungssituation = Gefahrenquelle (inkl. Gefährdungsbereich) + Gefährdung + Ereignis
Was wir an dieser Stelle noch erwähnen möchten ist, dass die Norm EN 12100 als auch die Maschinenrichtlinie die Risikobeurteilung für alle Lebensphasen des Produktes fordert. D.h. beginnend von der Anlieferung also dem Transport der Maschine bis zur Entsorgung. Wir empfehlen daher, die Risikobeurteilung auch entsprechend zu strukturieren.
Die Gefahrenquellen und ihre Gefährdungen
Dank der Ablaufbeschreibung wissen wir, wer was und wo in jeder Lebensphase zu tun hat. Nehmen wir jetzt ein Programm wie z.B. Excel können wir eine Tabelle wie folgt aufsetzen und befüllen sie in der Reihenfolge, die die bereits erstellte Ablaufbeschreibung vorgibt.
- Lebensphase
- Tätigkeit
- Gefährdung
- Gefahrenquelle
- Gefährdungsbereich
Wir berücksichtigen beim ausfüllen der Liste auch, dass in der Ablaufbeschreibungen Tätigkeiten parallel ausgeführt werden können. Damit ist gemeint, dass z.B. zwei Personen an einer Maschine arbeiten und die Tätigkeit des einen zur Gefährdung des anderen werden kann.
Zu jeder Tätigkeit stellen wir uns nun die Frage, was kann mir passieren wenn ich das mache. Die Antwort ist kurz und knapp "Folge durch Ursprung". Also z.B. tödlicher Stromschlag durch das Berühren eines spannungsführenden Teiles. Wir tragen also "tödlicher Stromschlag" bei Gefährdung ein und das Spannungsführende Teil bei Gefahrenquelle ein. Zusätzlich geben wir auch den Gefährdungsbereich an, der betroffen ist. In diesem Beispiel ist der Bereich auf die Quelle beschränkt. Besteht jedoch die Gefährdung von herumfliegenden Teilen, dann ist der Gefährdungsbereich wesentlich größer. Damit sind evtl. auch Personen betroffen, die nicht im direkten Zusammenhang mit dieser Tätigkeit stehen, jedoch nach Ablaufbeschreibung eine andere parallel in diesem Bereich ausführen.
Eintreten des Schadens durch Gefährdungsereignis
Lassen Sie uns nun die Tabelle um die beiden Spalten Gefahrenquelle und Gefährdung erweitern.
- Lebensphase
- Tätigkeit
- Gefährdung
- Gefahrenquelle
- Gefährdungsbereich
- Gefährdungsereignis
Damit es auch tatsächlich zu einem Schaden kommt, muss zusätzlich zur Gefährdung auch ein Gefährdungsereignis eintreten. Wir sind hier nicht nur auf ein Ereignis beschränkt, denn es können mehrere auftreten. Diese können unabhängig voneinander sein, oder auch in einer Verkettung vorliegen. Die EN 12100 stellt hierzu eine Liste von Gefährdungsereignissen bereit, die mindestens berücksichtigt werden müssen. Die möglichen Ereignisse entnehmen wir also der EN 12100, als auch der FMEA die wir bei der Erstellung und Gestaltung der Funktionen durchgeführt haben. Ebenso lassen wir uns auch nicht davon stören, dass die Liste vielleicht schon eine größere Dimension hat. Sortiert, bewertet und gefiltert wird später.
Bildung der Gefährdungssituation
Wir erweitern die Tabelle wieder um zwei Spalten mit den Überschriften Gefährdungssituation und Beschreibung. Die Gefährdungssituation ist im Grunde nur die Zusammenfassung von Gefahrenquelle, Gefährdung und Ereignis. Wenn wir jeder Gefahrenquelle, jeder Gefährdung und jedem Ereignis eine ID zur eindeutigen Kennzeichnung hinzufügen, haben wir damit auch eine Kodierung für die Gefährdungssituation erwirkt. Mit dieser lässt sich die Tabelle leicht filtern und zusammenfassen. Wir werden merken, dass sich die Gefährdungssituationen häufig wiederholen werden. D.h. unterschiedliche Tätigkeiten, sowie auch Lebensphasen können zur selben Gefährdungssituation führen.
- Lebensphase
- Tätigkeit
- Gefährdung
- Gefahrenquelle
- Gefährdungsbereich
- Gefährdungsereignis
- Gefährdungssituation
- Beschreibung
Mit der Spalte Beschreibung können wir die Situation auch in Prosa beschreiben um Missverständnisse bei der Interpretation zu vermeiden. Eine Formulierung kann wie folgt lauten:
Bei der Tätigkeit, besteht an der Gefahrenquelle xy innerhalb des Gefährdungsbereiches xy die Gefährdung durch einen tödlichen Stromschlag, wenn das Ereignis xy eintritt.
Wie auch von der EN 12100 gefordert, haben wir mit dem oberen Ablauf alle Gefährdungen, Gefährdungsereignisse und den damit zusammenhängenden Gefährdungssituationen ermittelt. Im folgenden gilt es, die identifizierten Gefährdungssituationen auf ihr Schadensausmaß und ihrer Eintrittswahrscheinlichkeit einzuschätzen. Diese Einschätzung soll uns im späteren Verlauf dazu dienen, zu bewerten, welche Gefährdungssituationen Maßnahmen zur Risikominimierung erfordern und in welcher Qualität. Die ist nach EN 12100 dann Aufgabe der Risikoeinschätzung, den wir in Teil 2 dieses Artikels behandeln werden und möchten.
Quellen:
[1] EN ISO 12100:2010 Sicherheit von Maschinen - Allgemeine Gestaltungsleitsätze - Risikobeurteilung und Risikominderung
[2] Richtlinie 2006/42/EG des Europäischen Parlaments und des Rates vom 17 Mai 2006 über Maschinen und zur Änderung der Richtlinie 95/16/EG
Kommentare
Diese Artikel hat nicht den Anspruch die EN 12100 an sich wieder zugeben. Vielmehr geht es hier darum ein besseres Verständnis zu schaffen und die Verwendung der EN 12100 zu fördern in dem dargestellt wird, dass sich die Risikobeurteilung effizient in einen Entwicklungsprozess integrieren lässt. Damit ist sie nicht separat zu betrachten, weder im Prozess noch in den Herstellungskosten. Wir hoffen, dass Sie sich Ihre benötigten Informationen aus diesem Artikel heraus nehmen konnten. Sollte Ihnen hier etwas fehlen oder der an einer bestimmten Stelle detailliertere Informationen benötigen, hinterlassen Sie uns doch eine Nachricht im Kommentarfeld.
Die Nachricht die Sie im Kommentarfeld abgeben wird auf dieser Seite angezeigt. Bitte geben Sie keine persönlichen Daten ein. Auf Wunsch werden selbstverständlich die entsprechenden Kommentare gelöscht.
Gerne können Sie Ihre Fragen alternativ auch an folgende Email-Adresse senden: team@searchnorm.de
Vielen Dank,
Team SearchNorm